The product and pouch variety of personal care, cosmetic, and refill products is enormous. Starting with small sachets for cream samples or portion sizes (single-serve), refreshing wipes or disinfectant wipes in pouches, and refilling pouches for liquid soaps or shampoos, the filling quantities range from a few milliliters for cream samples to 1,000 ml for refill pouches for liquid soaps. We can achieve the highest cycle outputs with high dosing accuracy and a wide range of viscosities using various dosing systems.
Precise filling
with the proper dosing technology
Almost all dosing systems can be integrated into our machines. Depending on the viscosity and product properties, different dosing systems are required, from small valve pumps to inductive flow meters. Certain dosing systems, especially smaller pump dosing systems, can also be carried out on trolleys for easier changing and cleaning. Self-cleaning (CIP) or sterilization (SIP) is possible for complex systems.
Precise filling combined with high cycle output ensures economical and efficient pouch packaging.
Flexibility
thanks to the variety in pouch shape and size
The different filling products also require different pouch shapes and sizes. For example, creams and lotions with filling quantities of a few milliliters are usually packaged in small sachets or flat pouches. Refill pouches for liquids of several hundred milliliters, such as liquid soap (500 ml) or shampoo (750 ml), are usually packed in stand-up pouches with or without a spout. Individual pouch contours are sometimes produced for unusual shapes and designs. We offer various machines suitable for various cosmetic and personal care products, as well as refill products. Precise filling combined with high cycle output ensures economical and efficient pouch packaging.
High flexibility and speed
Our machines can produce three-edge or four-edge sealed pouches, bottom-fold pouches, and stand-up pouches. Sealing in a spout, typically a corner spout, is also possible. Our machines can fill a wide range of fill weights. Many machines also offer various pouch formats so that many product variants can be packaged on the same machine. With a production speed of up to 100 cycles per minute, the products are filled and packaged highly economically.
Quick and easy format changes
Depending on the format and machine type, format changes can be made in just a few minutes and, in some cases, without tools. Production and machine parameters for individual products and formats can be quickly loaded automatically in the operating panel (HMI) via integrated recipe management. Short format and product changeover times significantly reduce the machine's non-production time (downtime), ultimately ensuring higher machine utilization and greater productivity.
Low space requirement thanks to the rotary principle
We have always stood for horizontal rotary machines (HFFS/HFS). This machine principle requires tiny production space, mainly due to working with a rotary table. We can supply you with pouch packaging machines with integrated dosing systems from a footprint of 20 m².
High-quality products deserve premium pouch quality
The essence of designing a pouch
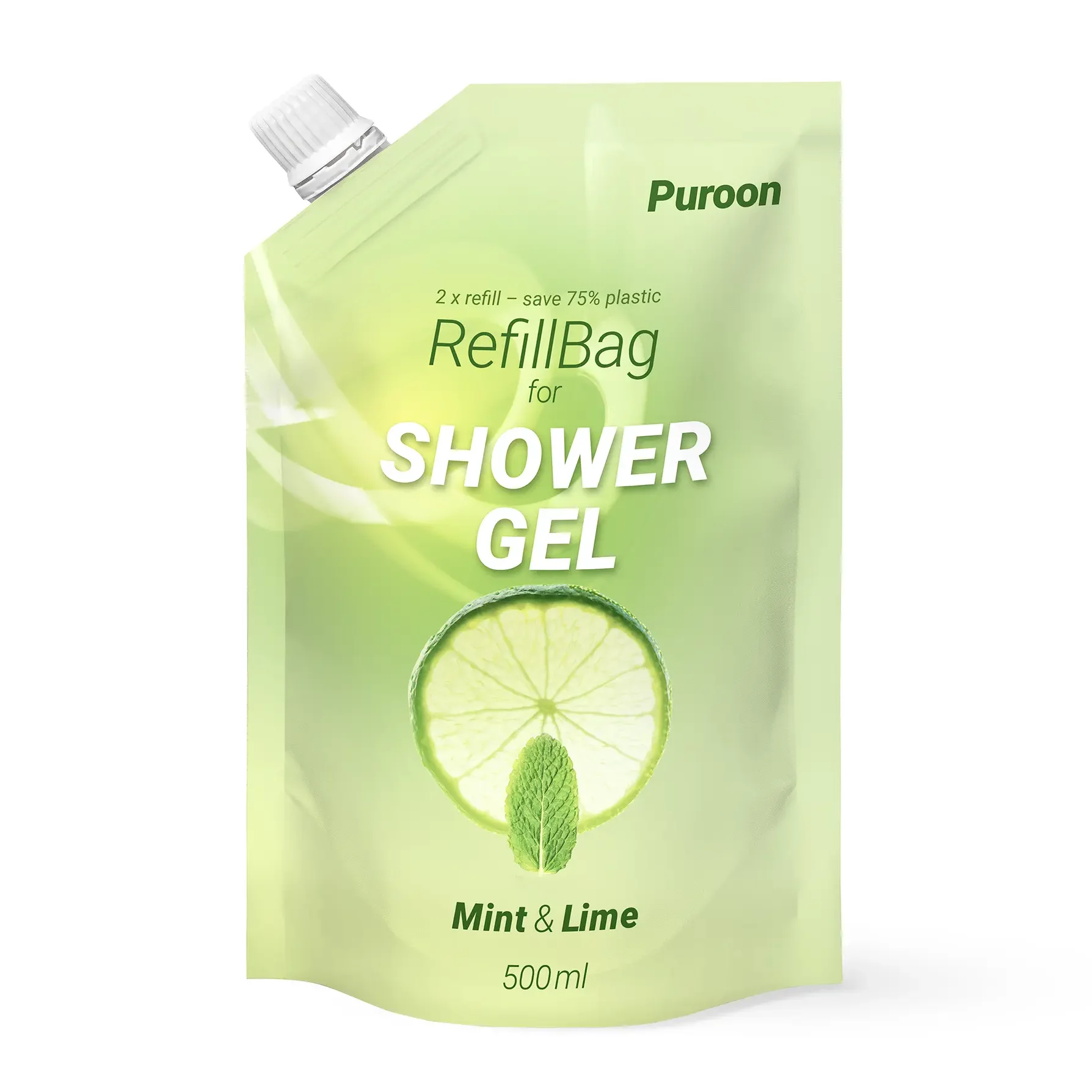
Stand-up bottom
An additional fold in the packaging material creates a pouch's stand-up base. This very stable base construction enables the pouch to stand independently on a flat surface. In addition to the primary function of being able to stand on its own, the stand-up bottom and the resulting bottom fold give the pouch a higher filling volume than a flat pouch. The bottom shape can usually be round, as in doypacks, or trapezoidal, as in deltapacks.
Side sealing seam
The side sealing seam is the two sealed pouch edges and closes it in this area. The side sealing seam requires exceptional quality and strength. Its width can be freely selected according to the length of the pouch. Depending on the contents, filling quantity, and size, the pouch must be able to withstand various pressures and sealing requirements. Optical and functional sealing patterns, such as cross and ripple patterns, can also be created in the sealing seam.
Top sealing seam
A top sealing seam permanently closes the pouch after filling. The side sealing seam requires exceptional quality and strength. Depending on the contents, filling quantity, and size, the pouch must be able to withstand various pressures and tightness requirements. In addition to the technical requirements, wider top sealing seams are often produced to give the pouch a corresponding appearance. Additional functions like hanging devices (euro hole or round hole) are integrated into the top seam.
Sealing seam quality
Sealing seam quality is one of a pouch core criteria. It must meet a wide range of quality and functional criteria. Thanks to our innovative and high-quality sealing technology, our machines can guarantee consistently high sealing seam strength over the long term. This also applies to different packaging materials and mono-materials.
Processability of mono-materials
All of our new machines can process recyclable mono-materials as standard. Thanks to innovative unwinding and sealing technology, new and thinner films and papers can be processed at the same quality and speed.
Filling level
To minimize packaging material and costs, but also from a sustainability perspective, keeping the space between the product fill level and the top sealing seam as small as possible is essential. Some technical processes, such as tightening before head sealing, require a certain amount of space in the headspace of the pouch. Headspace steaming, intended to counteract possible pouch inflation, also requires a certain amount of free space in the head area of the pouch. We are happy to help with the optimum design of the pouch dimensions depending on the intended filling quantity and filling level.
Spout
Sealing a spout into the pouch top seam is advisable for pouring the pouch contents single-use or multiple times. The spout can be sealed in the center or the corner of the pouch and the cap is used to reclose the pouch.
Overview of common pouch details
Details that really matter
-
Stand-up bottom
An additional fold in the packaging material creates a pouch's stand-up base. This very stable base construction enables the pouch to stand independently on a flat surface. In addition to the primary function of being able to stand on its own, the stand-up bottom and the resulting bottom fold give the pouch a higher filling volume than a flat pouch. The bottom shape can usually be round, as in doypacks, or trapezoidal, as in deltapacks.
-
Side sealing seam
The side sealing seam is the two sealed pouch edges and closes it in this area. The side sealing seam requires exceptional quality and strength. Its width can be freely selected according to the length of the pouch. Depending on the contents, filling quantity, and size, the pouch must be able to withstand various pressures and sealing requirements. Optical and functional sealing patterns, such as cross and ripple patterns, can also be created in the sealing seam.
-
Top sealing seam
A top sealing seam permanently closes the pouch after filling. The side sealing seam requires exceptional quality and strength. Depending on the contents, filling quantity, and size, the pouch must be able to withstand various pressures and tightness requirements. In addition to the technical requirements, wider top sealing seams are often produced to give the pouch a corresponding appearance. Additional functions like hanging devices (euro hole or round hole) are integrated into the top seam.
-
Sealing seam quality
Sealing seam quality is one of a pouch core criteria. It must meet a wide range of quality and functional criteria. Thanks to our innovative and high-quality sealing technology, our machines can guarantee consistently high sealing seam strength over the long term. This also applies to different packaging materials and mono-materials.
-
Processability of mono-materials
All of our new machines can process recyclable mono-materials as standard. Thanks to innovative unwinding and sealing technology, new and thinner films and papers can be processed at the same quality and speed.
-
Filling level
To minimize packaging material and costs, but also from a sustainability perspective, keeping the space between the product fill level and the top sealing seam as small as possible is essential. Some technical processes, such as tightening before head sealing, require a certain amount of space in the headspace of the pouch. Headspace steaming, intended to counteract possible pouch inflation, also requires a certain amount of free space in the head area of the pouch. We are happy to help with the optimum design of the pouch dimensions depending on the intended filling quantity and filling level.
-
Spout
Sealing a spout into the pouch top seam is advisable for pouring the pouch contents single-use or multiple times. The spout can be sealed in the center or the corner of the pouch and the cap is used to reclose the pouch.
We are happy to support you in your pouch packaging project with customized machine and dosing technology.
We look forward to your inquiry.
Phone: +49 2267 699-0
Email: sales@sn-packaging.de
FME 50
Horizontal form, fill, and seal machine (HFFS)
for 3-/4-side seal pouches
Format range pouch width
50 – 170 mm
Format range pouch height
70 – 210 mm
Realistic output rate
up to 100 pouches/min.
Exemplary yearly production output (single shift)
about 10.5 million pouches
(Data dependent on filling properties, pouch size, material, and production times)
FM 060
Horizontal form, fill, and seal machine (HFFS)
simplex for corner spout pouches
Format range pouch width
40 – 220 mm
Format range pouch height
50 – 250 mm
Realistic output rate
up to 60 pouches/min.
Exemplary yearly production output (single shift)
about 6.5 million pouches
(Data dependent on fillinf properties, pouch size, material, and production times)
LMS 120
Horizontal form, fill, and seal machine (HFFS)
simplex for corner spout pouches
Format range pouch width
50 – 200 mm
Format range pouch height
80 – 350 mm
Realistic output rate
up to 60 pouches/min.
Exemplary yearly production output (single shift)
about 20 million pouches
(Data dependent on filling properties, pouch size, material, and production times)
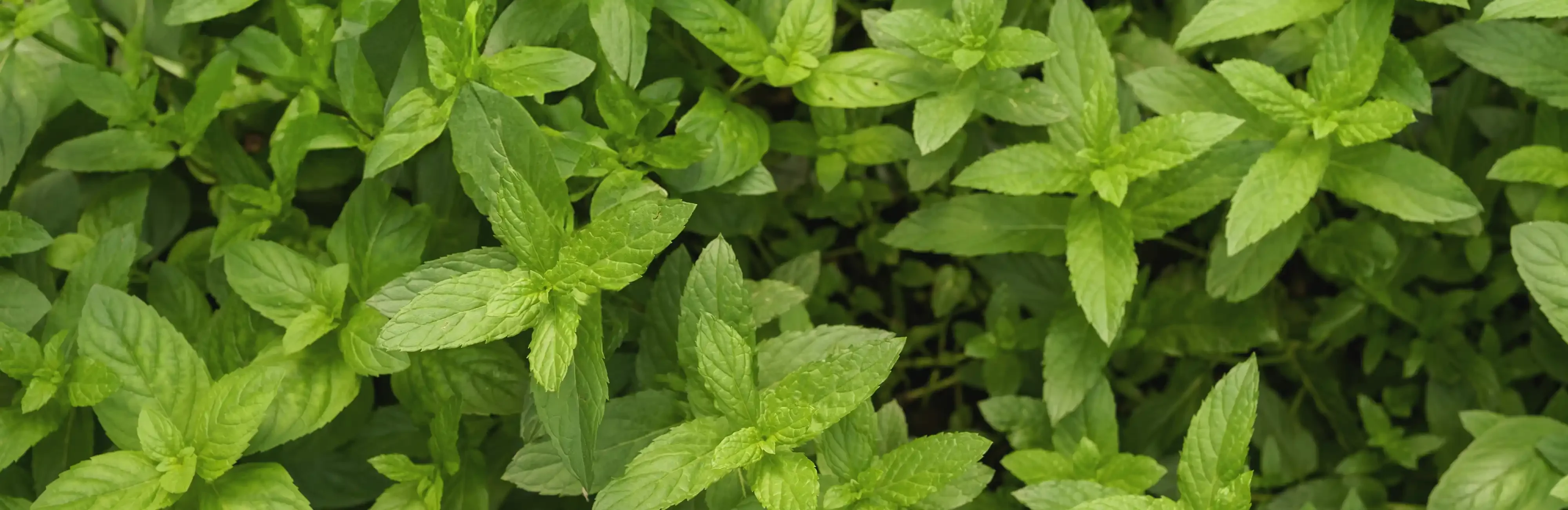
Contact
We are happy to support you in your pouch packaging project with customized machine and dosing technology.
We look forward to your inquiry.
Phone: +49 2267 699-0
Email: sales@sn-packaging.de