The filling and packaging of shredded cheese require the highest hygiene standards from the pouch packaging machine. Shredded cheese will usually be filled using multihead weighers that combine the target weight from individual weights. For example, the machine and dosing system must be cleaned frequently and intensively to prevent contamination and germs. To achieve maximum product shelf-life and product freshness in the pouch, residual oxygen will be reduced to a minimum.
With decades of experience and many machines on the market, we supply the perfect pouch packaging technology for shredded cheese. Our machines combine the highest quality standards with precise dosing technology and maximum speed. We aim to produce perfect pouches at the lowest unit costs and reliably over the machine's entire lifetime.
High output for every fill weight
via smart discharge management of the multihead weigher
Combined with multihead weighers, our machines achieve maximum cycle outputs with high filling quantities. With the help of smart discharge management, our machine waits for small delays in the multihead weigher and thus ensures more filled and sealable pouches. For larger product quantities, such as 500 grams, 750 grams, or 1,000 grams, filling can be divided between two stations. This means that short filling times per station can be maintained and high speeds achieved.
Processing thin films
Our innovative solutions enable processing the thinnest recyclable packaging films for shredded cheese. Continuous film unwinding reduces the stress on the packaging material by up to 70 %. The ability to process extremely thin films means immediate savings in packaging material and a significant cost reduction.
High flexibility
Our machines produce three-edge or four-edge sealed pouches, as well as bottom-fold and stand-up pouches. Resealing, such as zippers, is also possible. A wide range of filling weights can be filled. On request, the machine can be converted from simplex to duplex formats or duplex to triplex.
Quick and easy format changes
Depending on the format and machine type, format changes can be made in just a few minutes without tools. Production and machine parameters for individual products and formats can easily be load automatically in the operating panel (HMI) via integrated recipe management. Short format and product changeover times significantly reduce the non-production time (downtime) and ultimately ensure higher machine utilization and greater productivity.
Low space requirement due to the rotary principle
We have always stood for horizontal rotary machines (HFFS). This machine principle requires little space in production, particularly when working with a rotary table. We can supply you with pouch packaging machines with integrated dosing systems from a footprint of 20 m².
The space advantages of our rotary machines become increasingly apparent, especially with multiple machines.
Furthermore, the control cabinet can also be integrated into certain machine models, which simplifies the handling and commissioning of the machine, saves space compared to an external control cabinet, and improves accessibility.
Premium products deserve premium pouch quality
The essence of designing a pouch
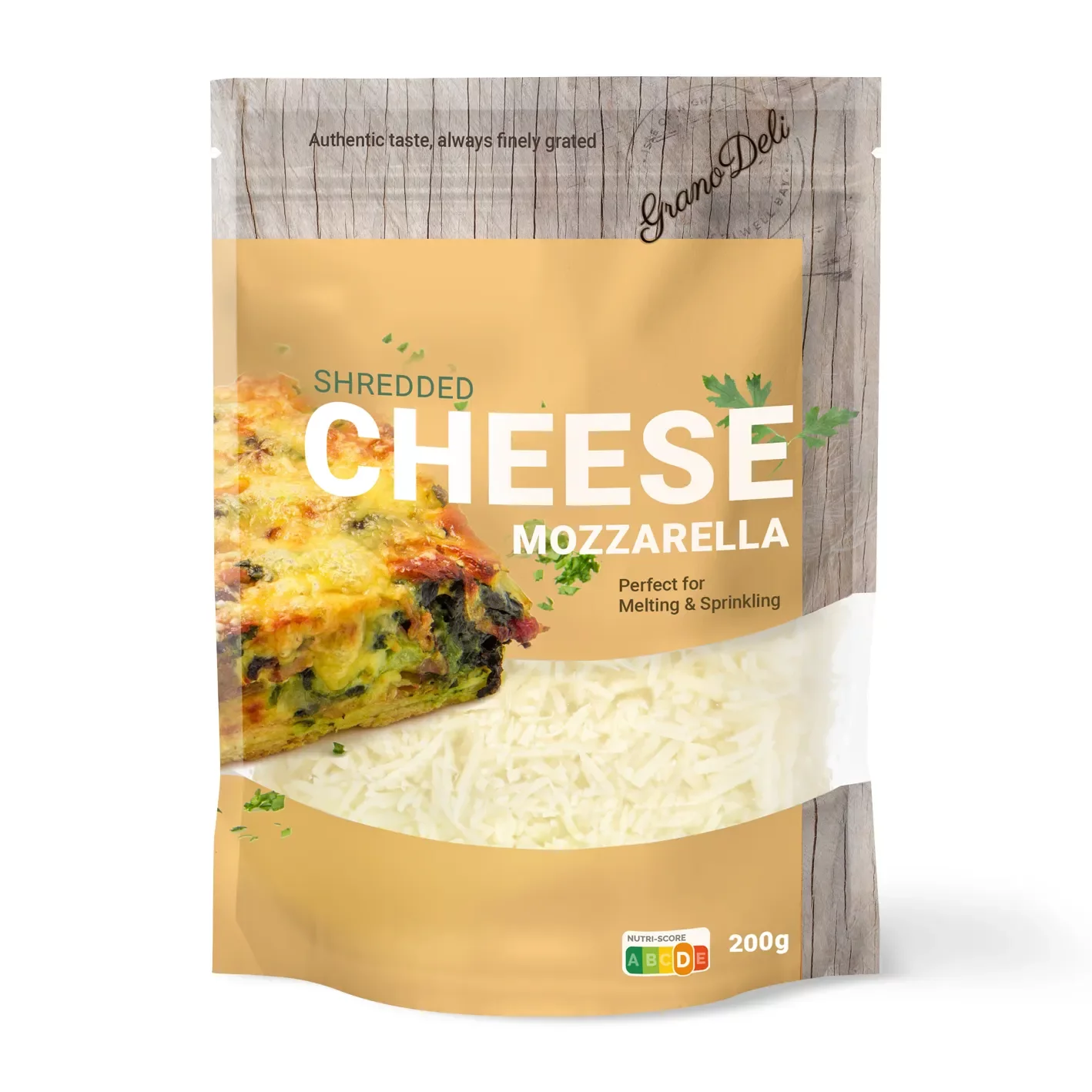
Stand-up bottom
An additional fold in the packaging material creates a pouch's stand-up base. This very stable base construction enables the pouch to stand independently on a flat surface. In addition to the primary function of being able to stand on its own, the stand-up bottom and the resulting bottom fold give the pouch a higher filling volume than a flat pouch. The bottom shape can usually be round, as in doypacks, or trapezoidal, as in deltapacks.
Zipper
A so-called zipper reclosure is often used to make the pouch reclosable. This zipper consists of two plastic lips that can be pressed together, pulled apart, and sealed into the top area of the pouch. This makes it possible to reclose the pouch after it has been opened for the first time and maintain the filling product's freshness to a certain extent.
Tear opening notch
The tear-opening notch is a punched hole in the upper side seal seam of the pouch. This punching makes it easier for the consumer to tear open the pouch without tools and consume the contents. The tear-opening notch is usually designed as an incision or punched-out arrowhead.
Side sealing seam
The side sealing seam is the two sealed pouch edges and closes it in this area. The side sealing seam requires exceptional quality and strength. Its width can be freely selected according to the length of the pouch. Depending on the contents, filling quantity, and size, the pouch must be able to withstand various pressures and sealing requirements. Optical and functional sealing patterns, such as cross and ripple patterns, can also be created in the sealing seam.
Top sealing seam
A top sealing seam permanently closes the pouch after filling. The side sealing seam requires exceptional quality and strength. Depending on the contents, filling quantity, and size, the pouch must be able to withstand various pressures and tightness requirements. In addition to the technical requirements, wider top sealing seams are often produced to give the pouch a corresponding appearance. Additional functions like hanging devices (euro hole or round hole) are integrated into the top seam.
Sealing seam quality
Sealing seam quality is one of a pouch`s core criteria. It must meet a wide range of quality and functional criteria. Thanks to our innovative and high-quality sealing technology, our machines can guarantee consistently high sealing seam strength over the long term. This also applies to different packaging materials and mono-materials.
Processability of mono-materials
All of our new machines can process recyclable mono-materials as standard. Thanks to innovative unwinding and sealing technology, new and thinner films and papers can be processed at the same quality and speed.
Filling level
To minimize packaging material and costs, but also from a sustainability perspective, keeping the space between the product fill level and the top seam as small as possible is essential. Some technical processes, such as tightening before head sealing, require a certain amount of space in the headspace of the pouch. Headspace steaming, intended to counteract possible pouch inflation, also requires a certain amount of free space in the head area of the pouch. We are happy to help with the optimum design of the pouch dimensions depending on the intended filling quantity and filling level.
Overview of common pouch details
Details that really matter
-
Stand-up bottom
An additional fold in the packaging material creates a pouch's stand-up base. This very stable base construction enables the pouch to stand independently on a flat surface. In addition to the primary function of being able to stand on its own, the stand-up bottom and the resulting bottom fold give the pouch a higher filling volume than a flat pouch. The bottom shape can usually be round, as in doypacks, or trapezoidal, as in deltapacks.
-
Zipper
A so-called zipper reclosure is often used to make the pouch reclosable. This zipper consists of two plastic lips that can be pressed together, pulled apart, and sealed into the top area of the pouch. This makes it possible to reclose the pouch after it has been opened for the first time and maintain the filling product's freshness to a certain extent.
-
Tear opening notch
The tear-opening notch is a punched hole in the upper side seal seam of the pouch. This punching makes it easier for the consumer to tear open the pouch without tools and consume the contents. The tear-opening notch is usually designed as an incision or punched-out arrowhead.
-
Side sealing seam
The side sealing seam is the two sealed pouch edges and closes it in this area. The side sealing seam requires exceptional quality and strength. Its width can be freely selected according to the length of the pouch. Depending on the contents, filling quantity, and size, the pouch must be able to withstand various pressures and sealing requirements. Optical and functional sealing patterns, such as cross and ripple patterns, can also be created in the sealing seam.
-
Top sealing seam
A top sealing seam permanently closes the pouch after filling. The side sealing seam requires exceptional quality and strength. Depending on the contents, filling quantity, and size, the pouch must be able to withstand various pressures and tightness requirements. In addition to the technical requirements, wider top sealing seams are often produced to give the pouch a corresponding appearance. Additional functions like hanging devices (euro hole or round hole) are integrated into the top seam.
-
Sealing seam quality
Sealing seam quality is one of a pouch`s core criteria. It must meet a wide range of quality and functional criteria. Thanks to our innovative and high-quality sealing technology, our machines can guarantee consistently high sealing seam strength over the long term. This also applies to different packaging materials and mono-materials.
-
Processability of mono-materials
All of our new machines can process recyclable mono-materials as standard. Thanks to innovative unwinding and sealing technology, new and thinner films and papers can be processed at the same quality and speed.
-
Filling level
To minimize packaging material and costs, but also from a sustainability perspective, keeping the space between the product fill level and the top seam as small as possible is essential. Some technical processes, such as tightening before head sealing, require a certain amount of space in the headspace of the pouch. Headspace steaming, intended to counteract possible pouch inflation, also requires a certain amount of free space in the head area of the pouch. We are happy to help with the optimum design of the pouch dimensions depending on the intended filling quantity and filling level.
We are happy to support you in your pouch packaging project with customized machine and dosing technology.
We look forward to your inquiry.
Phone: +49 2267 699-0
Email: sales@sn-packaging.de
FM 060
Horizontal form, fill and seal machine (HFFS) simplex
Format range pouch width
40 – 220 mm
Format range pouch height
50 – 250 mm
Realistic output rate
up to 65 pouches/min.
JExemplary yearly production output (single shift)
about 6 million pouches
(Data dependent on filling properties, pouch size, and production times)
FBM 22
Horizontal form, fill and seal machine (HFFS) duplex
Format range pouch width
120 – 190 mm
Format range pouch height
100 – 450 mm
Realistic output rate
up to 130 pouches/min.
Exemplary yearly production output (single shift)
about 14 million pouches
(Data dependent on filling properties, pouch size, and production times)
FMH 300
Horizontal form, fill and seal machine (HFFS)
Format range pouch width
115 – 194 mm
Format range pouch height
80 – 350 mm
Realistic output rate
up to 180 pouches/min.
Exemplary yearly production output (three shifts)
about 55 million pouches
(Data dependent on filling properties, pouch size, and production times)
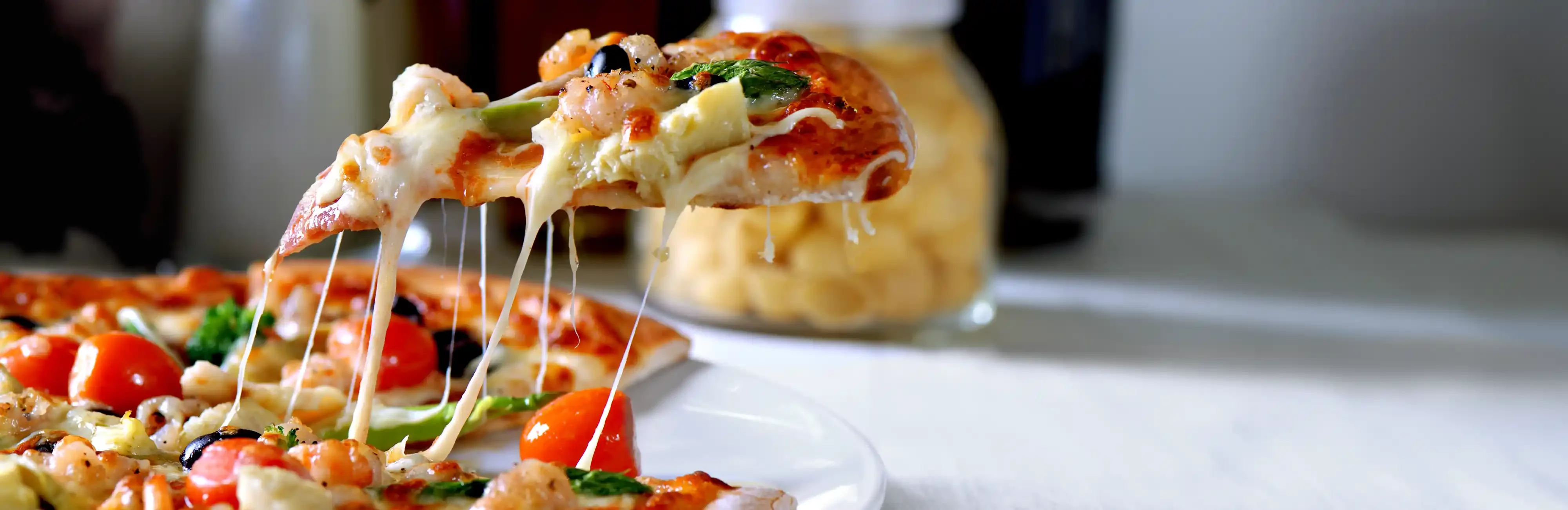
Contact
We are happy to support you in your pouch packaging project with customized machine and dosing technology.
We look forward to your inquiry.
Phone: +49 2267 699-0
Email: sales@sn-packaging.de