Fruit purees and pasty baby food are popular snacks for on-the-go. With a long shelf life, simple storage, and quick consumption straight from the spouted pouch, these snacks are suitable for on-the-go refreshments. They are available as an applesauce-based fruit mix in various varieties and as porridge with oat flakes, rice, or cereals. The requirements for pouch packaging with spouts for fruit purees and pasty baby food are particularly high.
The filling and packaging of these foods require special hygiene standards to avoid contamination and guarantee a product shelf life of over a year. The requirements for the packaging, such as film and spout, as well as the sealing quality, are particularly high here. Secure, tight, and high-performance sealing of the film and spout is essential here.
Clean and precise hot filling
via special dosing systems
Our packaging machines fill fruit puree and porridge quickly and cleanly into spouted pouches using specially developed dosing systems. The filling quantities usually range from 80 g to 200 g. For a maximum filling level in the pouch, we recommend filling through the spout. The product temperature of up to 95°C / 203°F is monitored during the entire process and packaging time to maintain the quality and shelf life of the product.
Maximum flexibility
for different varieties and tastes
Fruit puree and porridge come in many different varieties. Capable adapted pumps make it easy to fill different varieties in parallel and close them with various lids. That enables the direct production of product mixes for retailers and consumers. Product contamination in the sealing and spout areas can also avoided by filling separately from pouch production.
Performance on up to four lanes
Spouted pouches can be produced, filled, and sealed (FFS) on up to four lanes simultaneously with our high-performance pouch packaging machines for fruit puree. The performance spectrum ranges from simplex machines (1 pouch per cycle) with up to 4,200 pouches per hour to quadruplex machines (4 pouches per cycle) with a maximum of 14,500 pouches per hour. Various equipment options can be used to minimize downtimes, such as for reel changes, so machine efficiencies of up to 99% can be achieved.
Cleaning and hygiene
Special hygiene requirements must be applied when filling fruit puree and porridge. Contamination and product residue on the spout and cap must be avoided, particularly in the filling area. Filling through the spout avoids the risk of contamination in sealing areas and on the spout. Cleaning of the machine, product lines, and product feed is possible. The rotary piston doser, specially developed for fruit puree and porridge, can be easily cleaned (CIP) and sterilized (SIP) on the machine. The cleaning effort and -time can also be massively reduced by separating pouch production and pouch filling.
High flexibility
We offer various machine solutions for packaging and filling fruit puree and porridge in spouted pouches. From simplex to quadruplex, machine solutions are available for all output ranges (70-240 pouches/min.). Various products and spouts with differently colored lids can be run and packaged simultaneously on multi-lane machines. This allows product mixes to be produced easily and automatically in the machine.
Furthermore, inline solutions are possible, in which filling and pouch production are integrated into one machine, as well as the separation of pouch production and -filling. In this case, the filling methods are different because in inline operations, the pouch must be filled before the spout is added, whereas in separate operations, filling takes place through the spout, which leads to a significantly higher filling level and a reduction in the risk of contamination.
Premium pouch quality to go
The essence of designing a pouch
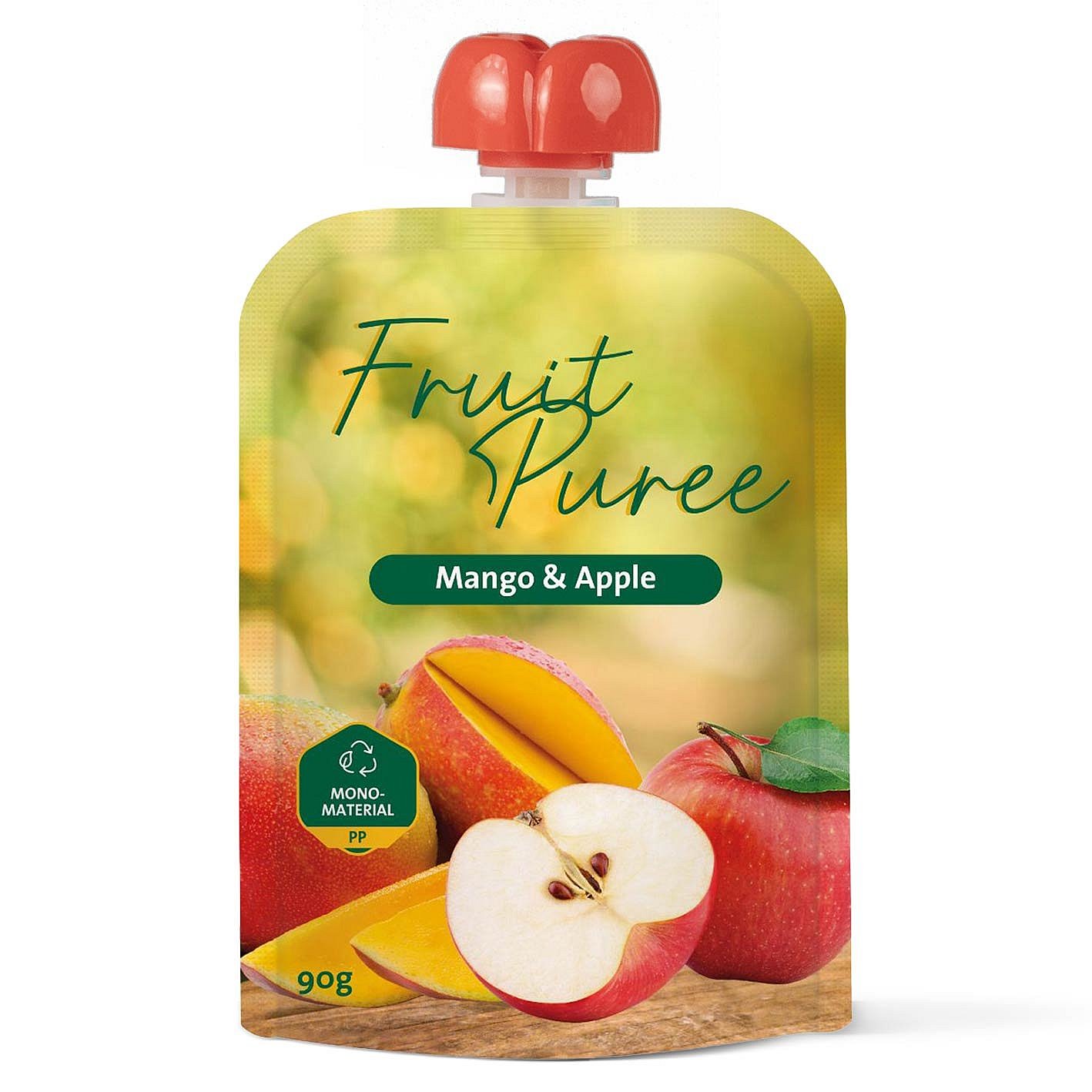
Stand-up bottom
An additional fold in the packaging material creates a pouch's stand-up base. This very stable base construction enables the pouch to stand independently on a flat surface. In addition to the primary function of being able to stand on its own, the stand-up bottom and the resulting bottom fold give the pouch a higher filling volume than a flat pouch. The bottom shape can usually be round, as in doypacks, or trapezoidal, as in deltapacks.
Side sealing seam
The side sealing seam is the two sealed pouch edges and closes it in this area. The side sealing seam requires exceptional quality and strength. Its width can be freely selected according to the length of the pouch. Depending on the contents, filling quantity, and size, the pouch must be able to withstand various pressures and sealing requirements. Optical and functional sealing patterns, such as cross and ripple patterns, can also be created in the sealing seam.
Top sealing seam
A top sealing seam permanently closes the pouch after filling. The side sealing seam requires exceptional quality and strength. Depending on the contents, filling quantity, and size, the pouch must be able to withstand various pressures and tightness requirements. In addition to the technical requirements, wider top sealing seams are often produced to give the pouch a corresponding appearance. Additional functions like hanging devices (euro hole or round hole) are integrated into the top seam.
Sealing seam quality
Sealing seam quality is one of a pouch core criteria. It must meet a wide range of quality and functional criteria. Thanks to our innovative and high-quality sealing technology, our machines can guarantee consistently high sealing seam strength over the long term. This also applies to different packaging materials and mono-materials.
Processability of mono-materials
All of our new machines can process recyclable mono-materials as standard. Thanks to innovative unwinding and sealing technology, new and thinner films and papers can be processed at the same quality and speed.
Filling level
To minimize packaging material and costs, but also from a sustainability perspective, keeping the space between the product fill level and the top sealing seam as small as possible is essential. Some technical processes, such as tightening before head sealing, require a certain amount of space in the headspace of the pouch. Headspace steaming, intended to counteract possible pouch inflation, also requires a certain amount of free space in the head area of the pouch. We are happy to help with the optimum design of the pouch dimensions depending on the intended filling quantity and filling level.
Spout
Sealing a spout into the pouch top seam is advisable for pouring the pouch contents single-use or multiple times. The spout can be sealed in the center or the corner of the pouch and the cap is used to reclose the pouch.
Overview of common pouch details
Details that really matter
-
Stand-up bottom
An additional fold in the packaging material creates a pouch's stand-up base. This very stable base construction enables the pouch to stand independently on a flat surface. In addition to the primary function of being able to stand on its own, the stand-up bottom and the resulting bottom fold give the pouch a higher filling volume than a flat pouch. The bottom shape can usually be round, as in doypacks, or trapezoidal, as in deltapacks.
-
Side sealing seam
The side sealing seam is the two sealed pouch edges and closes it in this area. The side sealing seam requires exceptional quality and strength. Its width can be freely selected according to the length of the pouch. Depending on the contents, filling quantity, and size, the pouch must be able to withstand various pressures and sealing requirements. Optical and functional sealing patterns, such as cross and ripple patterns, can also be created in the sealing seam.
-
Top sealing seam
A top sealing seam permanently closes the pouch after filling. The side sealing seam requires exceptional quality and strength. Depending on the contents, filling quantity, and size, the pouch must be able to withstand various pressures and tightness requirements. In addition to the technical requirements, wider top sealing seams are often produced to give the pouch a corresponding appearance. Additional functions like hanging devices (euro hole or round hole) are integrated into the top seam.
-
Sealing seam quality
Sealing seam quality is one of a pouch core criteria. It must meet a wide range of quality and functional criteria. Thanks to our innovative and high-quality sealing technology, our machines can guarantee consistently high sealing seam strength over the long term. This also applies to different packaging materials and mono-materials.
-
Processability of mono-materials
All of our new machines can process recyclable mono-materials as standard. Thanks to innovative unwinding and sealing technology, new and thinner films and papers can be processed at the same quality and speed.
-
Filling level
To minimize packaging material and costs, but also from a sustainability perspective, keeping the space between the product fill level and the top sealing seam as small as possible is essential. Some technical processes, such as tightening before head sealing, require a certain amount of space in the headspace of the pouch. Headspace steaming, intended to counteract possible pouch inflation, also requires a certain amount of free space in the head area of the pouch. We are happy to help with the optimum design of the pouch dimensions depending on the intended filling quantity and filling level.
-
Spout
Sealing a spout into the pouch top seam is advisable for pouring the pouch contents single-use or multiple times. The spout can be sealed in the center or the corner of the pouch and the cap is used to reclose the pouch.
We are happy to support you in your pouch packaging project with customized machine and dosing technology.
We look forward to your inquiry.
Phone: +49 2267 699-0
Email: sales@sn-packaging.de
SPM 50
Horizontal pouch packaging machine (PM)
for separate filling
Format range pouch width
80 – 100 mm
Format range pouch height
70 – 210 mm
Realistic output rate
up to 70 pouches/min.
Exemplary yearly production output (three shifts)
about 6,5 million pouches
(Data dependent on filling properties, pouch size, and production times)
HSF 400
Horizontal form, fill and seal machine (HFFS)
Format range pouch width
70 – 100 mm
Format range pouch height
90 – 250 mm
Realistic output rate
up to 240 pouches/min.
Exemplary yearly production output (three shifts)
about 76 million pouches
(Data dependent on filling properties, pouch size, and production times)
LMS 124
Horizontal form, fill and seal machine (HFFS)
Format range pouch width
50 – 100 mm
Format range pouch height
80 – 250 mm
Realistic output rate
up to 240 pouches/min.
Exemplary yearly production output (three shifts)
about 76 million pouches
(Data dependent on filling properties, pouch size, and production times)
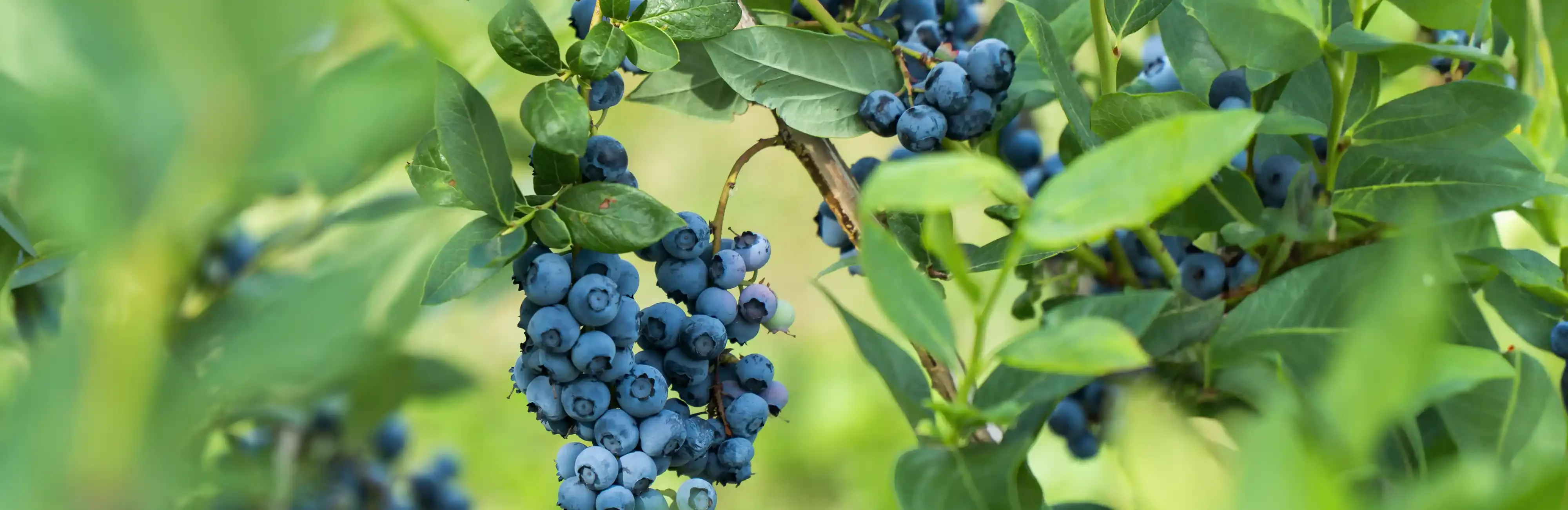
Contact
We are happy to support you in your pouch packaging project with customized machine and dosing technology.
We look forward to your inquiry.
Phone: +49 2267 699-0
Email: sales@sn-packaging.de