Packaging milk and protein powder places special demands on pouch packaging machines. We ensure that your powder product is packaged efficiently and cost effectively while eliminating the risk of dust and leaks. Avoiding product build-up on the outside of the pouch is also a concern for us. Our machines minimize the residual oxygen value in the pouch, which extends the shelf life of your products and reduces the risk of explosion by using the latest safety precautions. Our high-quality dosing technology ensures that each pouch contains the exact filling weight.
With decades of experience and many machines on the market, we supply the perfect pouch packaging technology. Our machines combine the highest quality standards with precise dosing technology and maximum speed. We aim to produce perfect pouches at the lowest unit costs and reliably over the machine's entire service life.
High flexibility
Our machines can produce small sachets, like three-sided or four-sided sealed pouches, as well as bottom-fold and stand-up pouches. The filling weights generally range from a few grams to several kilograms. In addition, sealing of a reclosure system, such as a zipper, is also possible. Another application-related highlight is the addition of a spoon into large pouches for easy dosing by the consumer.
Quick and easy format changes
Depending on the format and machine type, format changes are possible in just a few minutes and, in some cases, even without tools. Production and machine parameters for individual products and formats can easily be load in the operating panel (HMI) via integrated recipe management. Short format- and product changeover times significantly reduce the non-productive time (downtime) from the machine and ultimately ensure higher machine utilization and higher productivity.
Low space requirement due to the rotary principle
We have always stood for horizontal rotary machines (HFFS). This machine principle requires little space in production, particularly due to working with a rotary table. We can offer pouch packaging machines with integrated dosing systems with a base area of 20 m².
The space advantages of our rotary machines are becoming increasingly apparent, especially with multiple machines.
The control cabinet can also be integrated into certain machine models, which simplifies the handling and commissioning of the machine, saves space compared to an external control cabinet, and improves accessibility.
High-quality products deserve premium pouch quality
The essence of designing a pouch
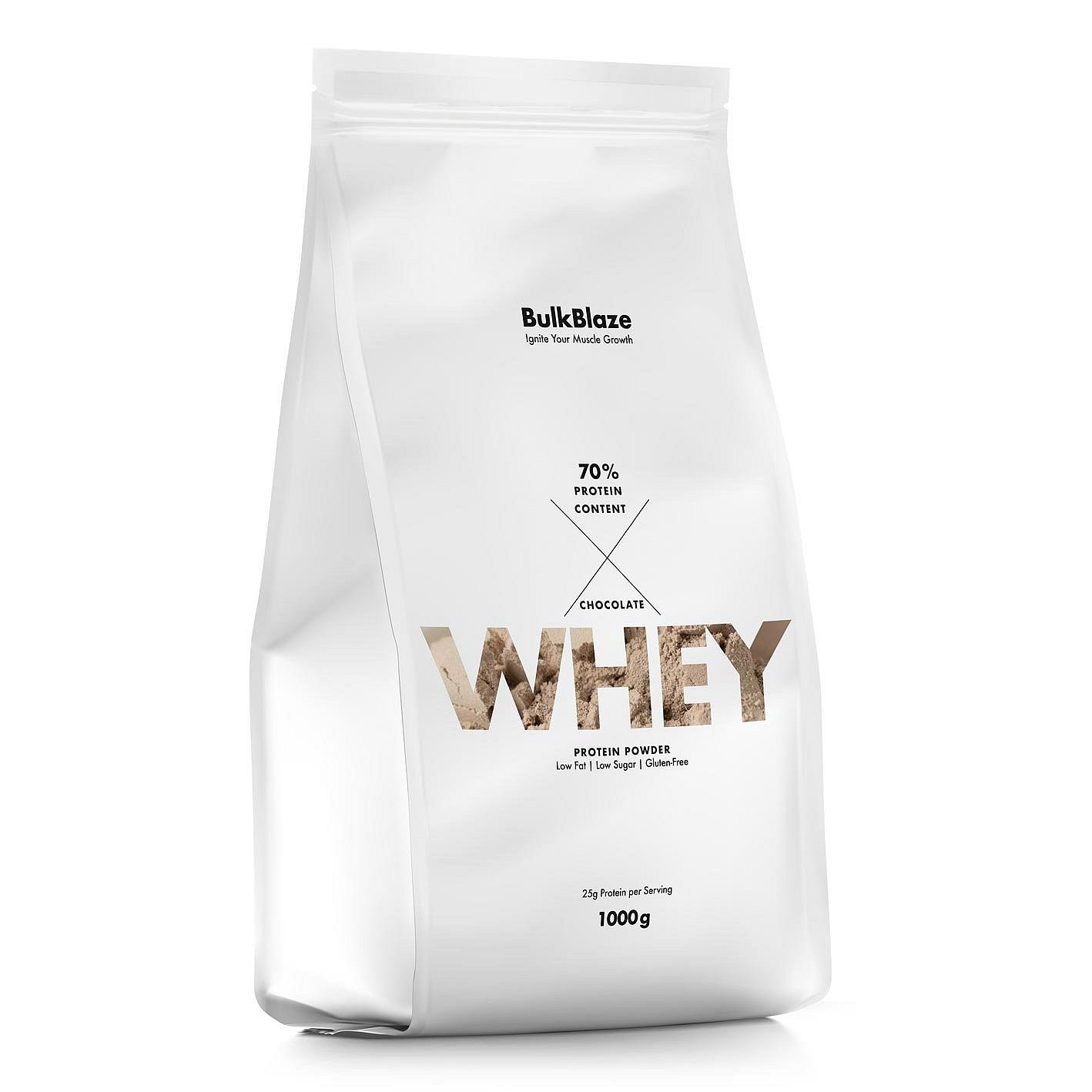
Stand-up bottom
An additional fold in the packaging material creates a pouch's stand-up base. This very stable base construction enables the pouch to stand independently on a flat surface. In addition to the primary function of being able to stand on its own, the stand-up bottom and the resulting bottom fold give the pouch a higher filling volume than a flat pouch. The bottom shape can usually be round, as in doypacks, or trapezoidal, as in deltapacks.
Zipper
A so-called zipper reclosure is often used to make the pouch reclosable. This zipper consists of two plastic lips that can be pressed together, pulled apart, and sealed into the top area of the pouch. This makes it possible to reclose the pouch after it has been opened for the first time and maintain the filling product's freshness to a certain extent.
Tear opening notch
The tear-opening notch is a punched hole in the upper side seal seam of the pouch. This punching makes it easier for the consumer to tear open the pouch without tools and consume the contents. The tear-opening notch is usually designed as an incision or punched-out arrowhead.
Side sealing seam
The side sealing seam is the two sealed pouch edges and closes it in this area. The side sealing seam requires exceptional quality and strength. Its width can be freely selected according to the length of the pouch. Depending on the contents, filling quantity, and size, the pouch must be able to withstand various pressures and sealing requirements. Optical and functional sealing patterns, such as cross and ripple patterns, can also be created in the sealing seam.
Top sealing seam
A top sealing seam permanently closes the pouch after filling. The side sealing seam requires exceptional quality and strength. Depending on the contents, filling quantity, and size, the pouch must be able to withstand various pressures and tightness requirements. In addition to the technical requirements, wider top sealing seams are often produced to give the pouch a corresponding appearance. Additional functions like hanging devices (euro hole or round hole) are integrated into the top seam.
Sealing seam quality
Sealing seam quality is one of a pouch core criteria. It must meet a wide range of quality and functional criteria. Thanks to our innovative and high-quality sealing technology, our machines can guarantee consistently high sealing seam strength over the long term. This also applies to different packaging materials and mono-materials.
Processability of mono-materials
All of our new machines can process recyclable mono-materials as standard. Thanks to innovative unwinding and sealing technology, new and thinner films and papers can be processed at the same quality and speed.
Overview of common pouch details
Details that really matter
-
Stand-up bottom
An additional fold in the packaging material creates a pouch's stand-up base. This very stable base construction enables the pouch to stand independently on a flat surface. In addition to the primary function of being able to stand on its own, the stand-up bottom and the resulting bottom fold give the pouch a higher filling volume than a flat pouch. The bottom shape can usually be round, as in doypacks, or trapezoidal, as in deltapacks.
-
Zipper
A so-called zipper reclosure is often used to make the pouch reclosable. This zipper consists of two plastic lips that can be pressed together, pulled apart, and sealed into the top area of the pouch. This makes it possible to reclose the pouch after it has been opened for the first time and maintain the filling product's freshness to a certain extent.
-
Tear opening notch
The tear-opening notch is a punched hole in the upper side seal seam of the pouch. This punching makes it easier for the consumer to tear open the pouch without tools and consume the contents. The tear-opening notch is usually designed as an incision or punched-out arrowhead.
-
Side sealing seam
The side sealing seam is the two sealed pouch edges and closes it in this area. The side sealing seam requires exceptional quality and strength. Its width can be freely selected according to the length of the pouch. Depending on the contents, filling quantity, and size, the pouch must be able to withstand various pressures and sealing requirements. Optical and functional sealing patterns, such as cross and ripple patterns, can also be created in the sealing seam.
-
Top sealing seam
A top sealing seam permanently closes the pouch after filling. The side sealing seam requires exceptional quality and strength. Depending on the contents, filling quantity, and size, the pouch must be able to withstand various pressures and tightness requirements. In addition to the technical requirements, wider top sealing seams are often produced to give the pouch a corresponding appearance. Additional functions like hanging devices (euro hole or round hole) are integrated into the top seam.
-
Sealing seam quality
Sealing seam quality is one of a pouch core criteria. It must meet a wide range of quality and functional criteria. Thanks to our innovative and high-quality sealing technology, our machines can guarantee consistently high sealing seam strength over the long term. This also applies to different packaging materials and mono-materials.
-
Processability of mono-materials
All of our new machines can process recyclable mono-materials as standard. Thanks to innovative unwinding and sealing technology, new and thinner films and papers can be processed at the same quality and speed.
We are happy to support you in your pouch packaging project with customized machine and dosing technology.
We look forward to your inquiry.
Phone: +49 2267 699-0
Email: sales@sn-packaging.de
FME 50
Horizontal form, fill and seal machine (HFFS)
Format range pouch width
50 – 170 mm
Format range pouch height
70 – 210 mm
Realistic output rate
up to 70 pouches/min.
Exemplary yearly production output (single shift)
about 6 million pouches
(Data dependent on filling properties, pouch size, and production times)
FBM 071
Horizontal form, fill and seal machine (HFFS) simplex
Format range pouch width
50 – 254 mm
Format range pouch height
80 – 350 mm
Realistic output rate
up to 70 pouches/mins
Exemplary yearly production output (single shift)
about 6 million pouches
(Data dependent on filling properties, pouch size, and production times)
FM 400
Horizontal form, fill and seal machine (HFFS)
Format range pouch width
80 – 137 mm
Format range pouch height
90 – 250 mm
Realistic output rate
up to 280 pouches/min.
Exemplary yearly production output (three shifts)
about 90 million pouches
(Data dependent on filling properties, pouch size, and production times)
When we received the delivered box, we were able to take the FME 50 out in one piece and essentially "plug and play". Drawings, dimensions, power and air specifications were provided prior to shipment so that everything was ready at our place when the shipment arrived from overseas. The few parts that required assembly upon arrival were self-explanatory or labeled for easy installation.
It only took one day of training from the supplier's technician and a few minor adjustments before our two operators could essentially operate the machine on their own. The machine ran very well right away and the quality was better than expected.
The FME 50 is intuitive and fairly easy to use. We at Origin Nutraceutical are happy that we opted for the recommended upgrades and automation features. This unit will be a great asset to us thanks to its speed, quality, clean operation and minimal operator requirements.
Our initial backlog of pouches was eliminated within a few weeks of smooth operation with our new FME 50 from SN Maschinenbau. Many thanks to everyone involved in this process."
Since we have been working closely with SN Maschinenbau for years, we had no concerns about buying the prototype of the new machine series. Minor modifications and start-up difficulties were discussed directly during the factory acceptance and our wishes were implemented immediately so that we could start production in our factory straight away. Overall, we are very satisfied with the FME 50 and the partnership with SN Maschinenbau."
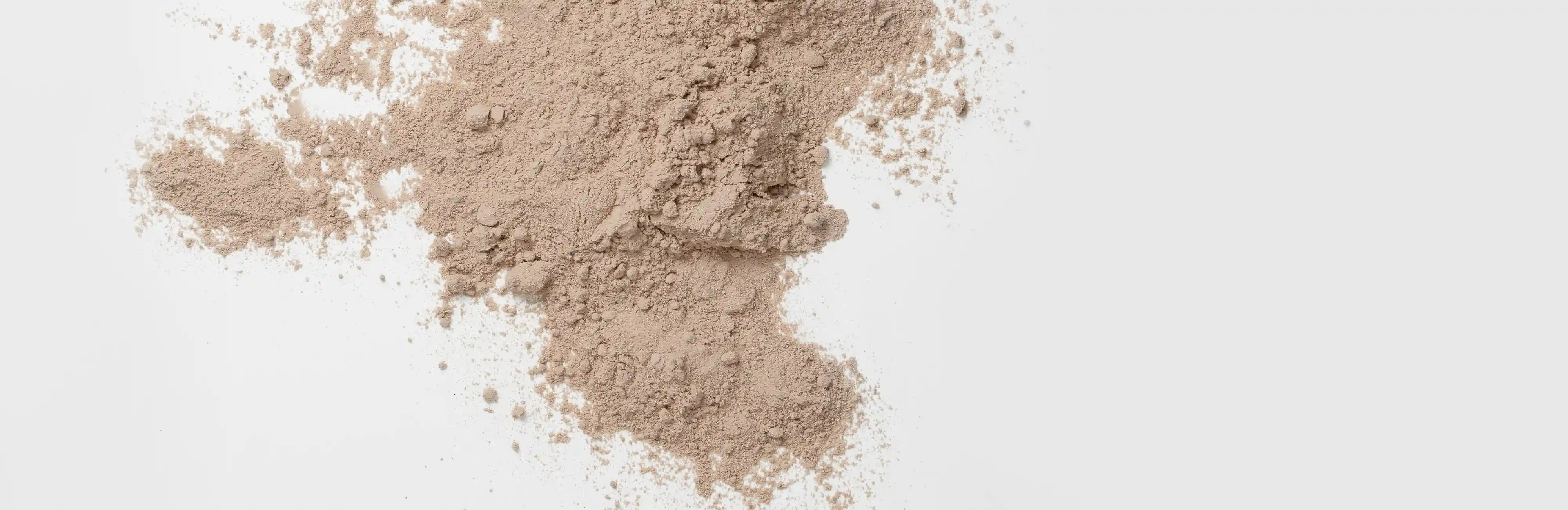
Contact
We are happy to support you in your pouch packaging project with customized machine and dosing technology.
We look forward to your inquiry.
Phone: +49 2267 699-0
Email: sales@sn-packaging.de